18 May 2021
This may be because I am fascinated with subterranean infrastructure, but I feel like tunnels have been all over the news lately. London’s Crossrail is now entering its final testing phase and Auckland’s new rail tunnel is beginning construction. A huge water project in Washington DC is almost complete, Norway is set to build the world’s first ship tunnel, and a pair of 1.3 km (0.8 mile)-long tunnels opened under the Las Vegas Convention Centre back in April.
Most of these headline-making projects share a common element. Excluding the ship tunnel, which will be excavated via many small, controlled explosions (in a process called ‘drilling and blasting’), the projects used tunnel boring machines (TBMs). These purpose-built cylindrical excavators – often nicknamed ‘moles’ – have been munching their way beneath our streets for many decades, giving us everything from small service pipelines to the world’s longest rail tunnel. They have become ubiquitous; the default option for tunnelling projects, especially those in built-up urban areas. Despite this, only a small fraction of city-dwellers ever get to see a TBM up close. So, I thought I might tell you a bit about how they work.
The general operating principle of a TBM is relatively simple. At the front, it has a rotating cutter head peppered with hard cutting bits – this is what ‘digs’, breaking up the rock or soil. The head is supported by the main bearing, and behind that is a thrust system – typically a ring of hydraulic cylinders or rams – that continuously push the head forward to advance the tunnelling. Behind that is a whole series of support structures. This includes a conveyer system to carry the excavated material from the cutter face, back through the tunnel to the exit, where it can be processed and transported for use elsewhere. As the cutter moves forward, it leaves smooth walls behind that can be lined with different materials. Large tunnels tend to use concrete segments which lock together to form rings – these are installed by an erector arm incorporated into the TBM. Other projects use precast concrete cylinders, coated in a low-friction clay, that are pushed into place behind the TBM by hydraulic rams at the tunnel entrance.
There are as many varieties of TBM as there are infrastructure projects, which means there are lots of specifics to consider.
For a start, there’s the diameter – how big do you want your tunnel to be? Until it was overtaken by the Tuen Mun - Chek Lap Kok TBM (which dug part of an undersea link between mainland China and Hong Kong International Airport), the world-record holder for girth was Bertha, the TBM used to build State Route 99’s double-decker road tunnel under Seattle. Bertha’s diameter was 17.5 m (~57.4 ft), just 0.1 m smaller than the current record holder. If I stacked six shipping containers on top of one another and clambered to the summit, I could only just reach the top of these enormous machines with my fingertips. At the other end of the scale are microtunnelling machines, which are available in diameters as small as 0.4 m, and which are widely used in wastewater and stormwater systems. In all cases, because a tunnel lining needs to be added during construction, a finished tunnel is always smaller than the TBM used to dig it.
The diameter also defines where the TBM will be piloted from. For large TBMs, typical of those used for road or rail tunnels, the pilot and a team of engineers work on-board the TBM itself, spread between a control box that sits behind the cutter head, and various platforms and gantries within the machine. For example, Alice, the TBM used to bore the Waterview road tunnel in Auckland, was crewed by 16 people at any one time. As you might expect, microtunnellers must be controlled from above ground, usually from a cabin positioned close to the tunnel entrance. Either way, driving a tunnelling machine involves a lot of software. More on that later.
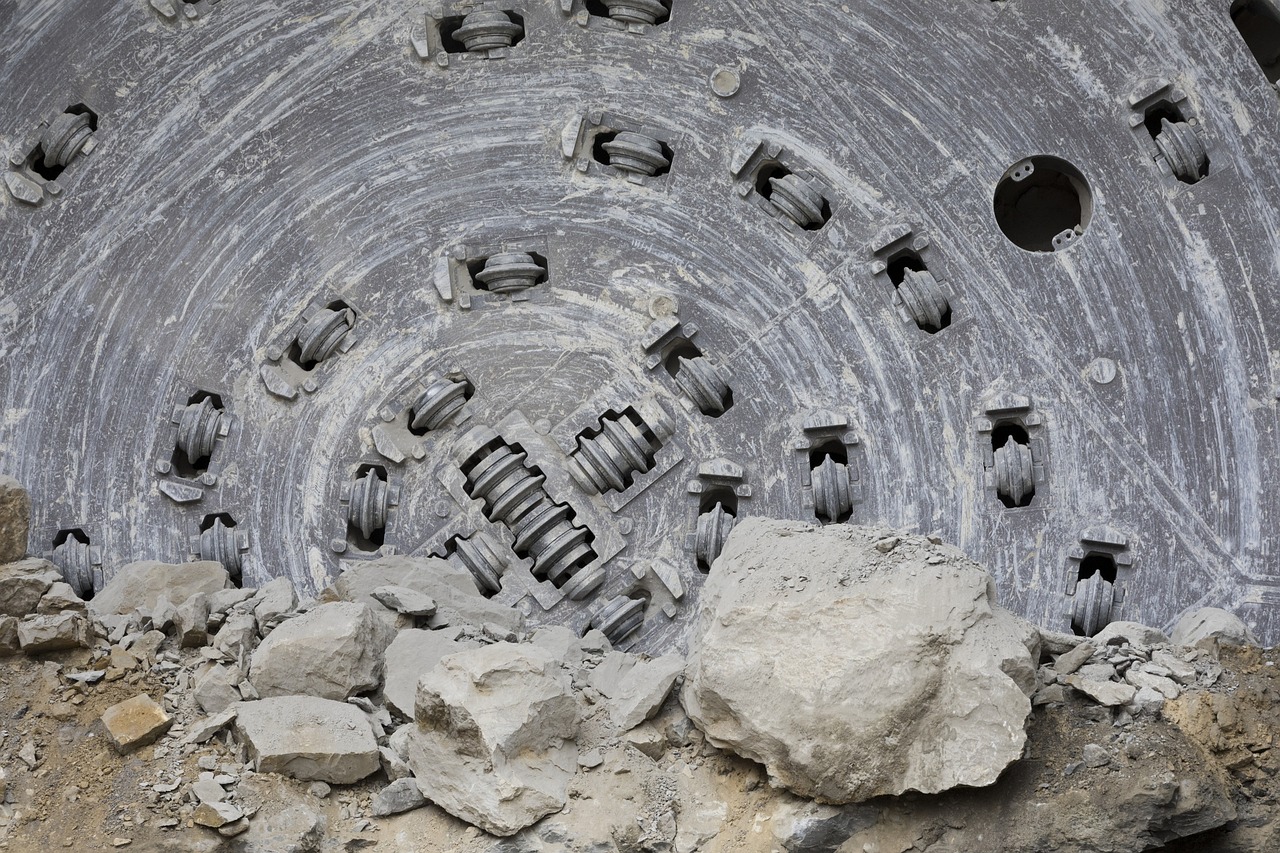
Once you know your diameter, the next thing to consider is the geology – what will the TBM have to cut through? This has an enormous impact both on the internal workings of a TBM, and on the materials used in its cutter head. For soft, dense, clay-like soils, you’ll probably want an Earth Pressure Balance Shield (EPB) TBM. Its name tells us a bit about how it works. As the cutter head rotates, it is pressed forward into the tunnel face. This produces a torque – a turning force – that, combined with a series of high-strength steel discs and teeth embedded in the cutter head, loosens the soil. To keep this process stable, the pressure inside the cutter head’s excavation chamber must be roughly equal to the pressure that the soil exerts on the cutter head. EPB TBMs do this by controlling both the quantity and the consistency of the excavated material in the chamber. Water, clay or foam can be injected into the material to help it flow, and the rotation rate of the screw conveyor – which carries the rock goo away – is matched to the advancing speed of the TBM. All the while, the pressures and torques involved are continuously monitored so that they can be adjusted and kept stable.
Of the eight TBMs used to dig Crossrail’s 42km of rail tunnels, six were EPBs. They were chosen precisely because the central section of the route passed through a geological layer called London Clay. Though too soft and prone to shrinkage to support lots of record-breaking skyscrapers above ground, its stability makes it the perfect material for subsurface structures like tunnels.
Crossrail’s other two TBMs, named Mary and Sophia, faced a different challenge. Their route crossed under the River Thames, which meant tunnelling through water-logged gravels and heterogeneous, sandy soils. In those conditions, slurry or mixshield TBMs were preferred because they’re designed to hold back the groundwater during the tunnelling process. The key to this is slightly overly-pressurising the two-part excavation chamber behind the cutter head. The front section is completely flooded with a mixture of bentonite clay and water. The connected rear section is partially filled with the same material, while a large air pocket occupies the rest of the space. As the tunnelling advances, this air pocket can be continuously compressed or expanded, depending on the pressure requirements. The excavated soil is fed through a one-way nozzle grid at the bottom of the cutterhead into a slurry line that pumps it away to the surface.
For all tunnelling projects – but especially those through hard rock, like granite – friction and stress are a key concern. TBM cutter heads get incredibly hot as they dig, with the cutter bits (teeth, wheels and discs) potentially reaching temperatures of 180 °C. These bits also have to survive the repeated impact of grinding into a rockface. TBM manufacturer Herrenknecht say that when tunnelling the Gotthard Base Tunnel deep under the Swiss Alps, “each of the 60 Cutter Disks….[were]…pushed into the mountain with a force of up to 27 tons.” If left unchecked, these loads can change the materials properties of the cutter teeth, wheels and discs, and ultimately cause them to fail. This is why ultra-hard steels alloyed with tungsten carbide are favoured in tunnelling projects. Integrated water-cooling systems and regular breaks in tunnelling help too, but even so, cutter bits don’t typically last for an entire project. Rather, they need to be replaced fairly regularly. For some TBMs, this can be done from inside the machine. For others, the cutter head needs to be retracted during a break in tunnelling, to provide workers with space to access it from the front (they clamber through a ‘trapdoor’ in the cutter face).
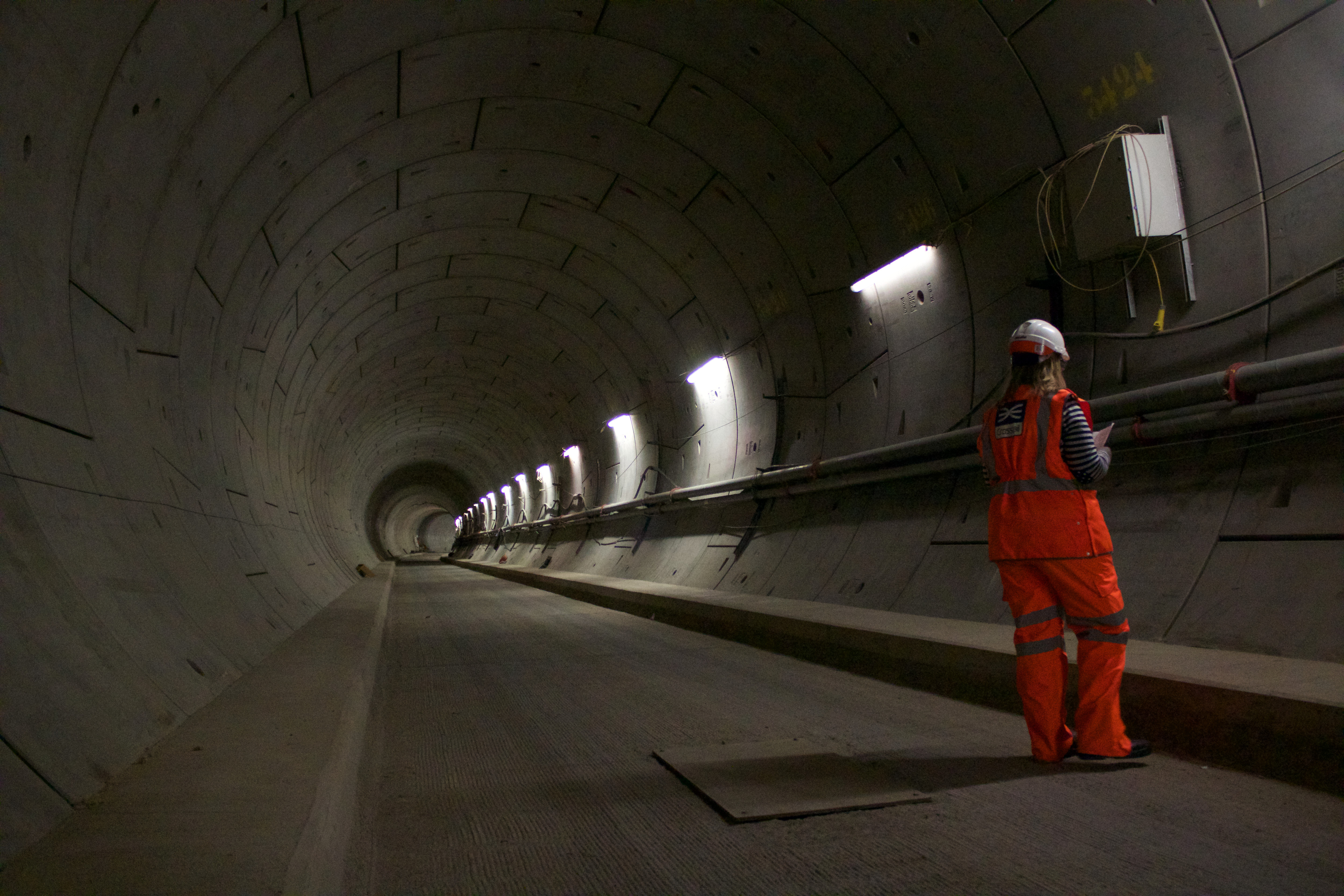
But even with the right machine, it’s rare that a city would ever sit atop pristine rock or soil. After all, most of today’s major urban centres occupy the same land as much earlier settlements, which has led to several tunnelling projects uncovering significant archaeological finds. There’s also more modern subterranean infrastructure to worry about. Your city might not have an underground rail or road tunnel, but it’s very likely to have water pipes, sewers, and power and internet lines below its streets. Any new tunnel will have to fit around what’s already there, and digging in such an environment requires precise control.
Take Tottenham Court Road tube station in central London, as an example. In 2014, Crossrail engineers steered a 1,000 tonne, 7.1 m (23.3 ft)diameter TBM through a triangular gap formed between its passenger escalators and the tube station platform tunnels. The margin of error was small, with a clearance of just 600 mm (23.6 in) above the existing tunnels, and 400 mm (15.75in) below the foundations of the escalators. No wonder the process has been described as “threading the eye of the needle”. Perhaps the most impressive thing of all is that they managed to thread this needle without disrupting tube services. On the days that TBM Ada was passing through, hundreds of thousands of passengers travelled on the escalators and boarded tube trains, unaffected by the dig.
This was achieved through a combination of detailed geotechnical surveys and 3D modelling (long before the digging started), and the sophisticated tracking and guidance systems on-board the TBM. Driving a TBM in a straight line is one thing, but if you want to steer it so that the tunnel curves left, right, up or down, you need to make careful adjustments to the thrust system –the ring of hydraulic cylinders around the circumference of the TBM. Rather than pushing equally across all of the cylinders, you apply an uneven pressure; similar to how pushing an object on its left-hand-side directs it to the right. This approach allows control of the TBM position to within ±5cm.
Laser-based tracking is also used to measure the constantly changing location of a TBM. It uses three main components: (1) a theodolite –effectively, a moveable telescope with an inbuilt laser – mounted onto the tunnel wall behind an advancing TBM; (2) a detector, installed on the back of the TBM – this is the target for the laser, and (3) a control unit that collects and analyses the data, and sends it to the control cab. This system provides the TBM pilot with a lot of vital information in real-time, including the distance travelled and the orientation of the cutter head. These can then be compared to the planned route. As the dig continues, with the tunnel often following a curving path, prisms are added to the walls – they deflect the laser around the curves and keep it pointing at the detector. Over larger distances, additional theodolites can be installed, providing a reliable reference chain for the TBM pilot to use for navigation.
Together, these technologies have allowed cities to expand downwards. Critical infrastructure that would otherwise dominate the landscape can now be buried deep underground. As a result, tunnels are easy to ignore; it’s very much a case of “out of sight, out of mind”. But in truth, tunnels – and the machines that build them – are engineering marvels that have played a vital role in shaping our urban landscapes. And now that you know them a little better, I hope it makes you a little less likely to take them for granted.
* Disclaimer: Five of the 17 links included in this piece direct to Herrenknecht AG’s website. I work with Herrenknecht on a range of different projects; however, this article is not part of any contract or agreement between us. I wrote it simply because I am obsessed with TBMs